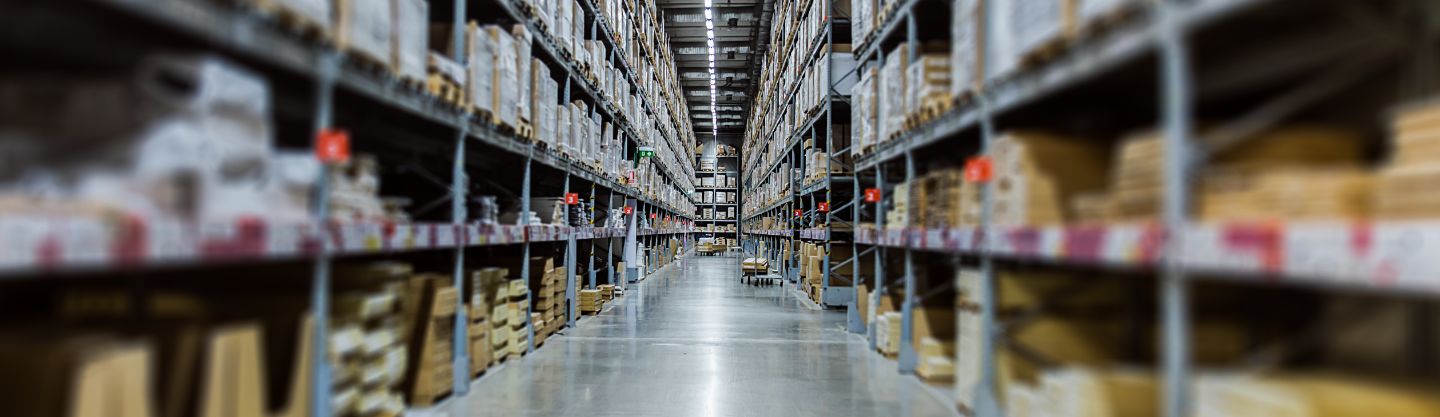
Building Supply Chain Resilience
Assessing the impact and resilience of York Region's manufacturing supply chain in response to COVID-19.
‘Building Supply Chain Resilience’ Report
To facilitate economic recovery and build manufacturing capacity and overall supply chain resilience, The Regional Municipality of York, in partnership with the cities of Markham, Richmond Hill and Vaughan (study co-sponsors), sought a deeper understanding of local manufacturing supply chain constraints, particularly within key industry verticals. To facilitate this work, they collaboratively engaged the support of Supply Chain Canada, and supply chain management consulting firm, Supply Chain Alliance.
Over several months, Supply Chain Alliance conducted detailed interviews with CEOs and supply chain and procurement leaders of York Region manufacturers in key sectors to identify COVID-19’s impact on their businesses, learn how these leaders responded, assess their state of readiness to the pandemic, and uncover any move-forward plans businesses have made to address future disruptions.
DOWNLOAD REPORT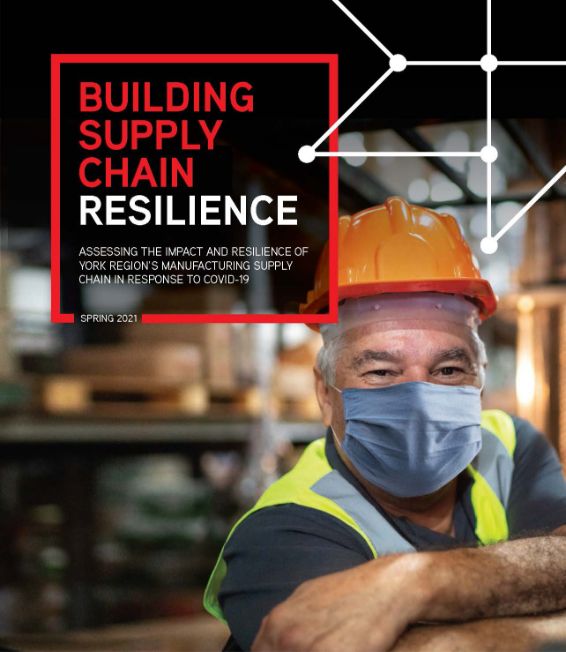
UNDERSTANDING THE LANDSCAPE
When COVID-19 hit and Canada launched its lockdown strategies at the federal, provincial and municipal levels, the manufacturing industry faced immediate impact. According to a recent Supply Chain Canada survey, 70% of Canadian supply chain professionals noted their organizations experienced supply chain disruptions as a direct result of COVID-19 implications. This was illustrated by the inability of government and industry to secure access to personal protective equipment (PPE) such as masks, gloves and sanitizer for frontline workers. Similar issues were experienced across the manufacturing process. As borders locked down around the world, the inflexibility of industrial globalization was clear. At the same time, the world was witnessing a rise in nationalism as many countries attempted to divert critical supplies for internal use by local populations.
In Canada, we saw the closure of non-essential businesses, which deeply impacted the country given approximately 40% of all imported goods are non-essential. As these inbound containers sat burdened with inventory for months, the natural flow of containers globally slowly began to congregate in non-traditional locations, resulting in container shortages at points of global embarkation and port congestion. To keep production running, York Region manufacturers turned to airfreight to access critical components that were produced offshore. They quickly found that available airfreight capacity was severely restricted and prohibitively expensive. Most goods are shipped in the cargo hold of passenger aircrafts; with passenger flights falling 85% during the pandemic, this created severe capacity constraints.
Finally, as the pandemic hit Canada, manufacturers faced non-traditional shifts in their demand with virtually no notice. Some industries, such as automotive, shut down completely in the first few months, while others like pharma, food and paper goods saw massive upswings due to consumer stockpiling. With short notice shifts in demand and long global supply chains for many manufacturing components, York Region manufacturers faced a myriad of challenges to navigate during the first two months of the pandemic, with many forced to pivot in order to survive.
A FRAMEWORK FOR SUCCESS
The study provides a framework of best practices that businesses can use when confronted with future supply chain disruptions. With respect to government recommendations, the study revealed York Region manufacturers would benefit from support from their different levels of government.